Integrated
Motion
Motion Control
Antriebstechniken
für die Zukunft
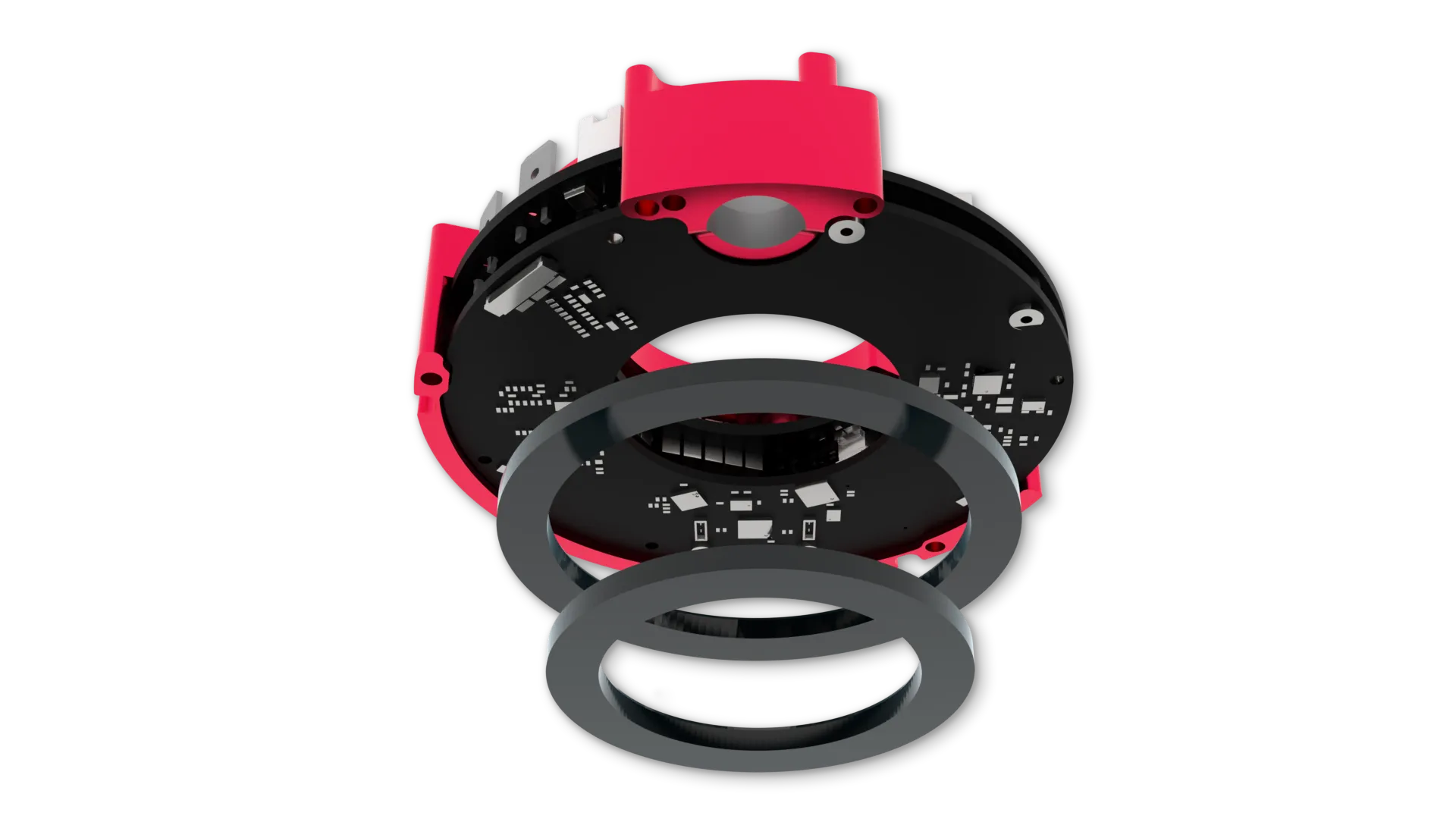
Servoantriebe und Antriebsregelungen sind die Gateways zwischen der virtuellen und der realen Welt. Es sind Sensoren und Antriebe, die einen Computer in einen Roboter verwandeln. Darum gilt bei uns Software-first-Prinzip.
Synapticon bietet ein umfassendes, weltweit führendes Portfolio von Technologien und Produkten im Bereich der industriellen, elektrischen Antriebsregelung. Wir entwickeln kompakte, hochintegrierte, effiziente und benutzerfreundliche Hochleistungs-Servoantriebe für Applikationen wie Roboter, Cobots und AGV / AMR. So entstehen zukunftsweisende Lösungen für die Integration von Motion Control in Bewegungsachsen. Die gesamte Technologie basiert auf dem SOMANET MOTION Software Stack. Synapticon ist das einzige "Software-First-Unternehmen" im Motion Control Bereich.
Synapticon bietet ein umfassendes, weltweit führendes Portfolio von Technologien und Produkten im Bereich der industriellen, elektrischen Antriebsregelung. Wir entwickeln kompakte, hochintegrierte, effiziente und benutzerfreundliche Hochleistungs-Servoantriebe für Applikationen wie Roboter, Cobots und AGV / AMR. So entstehen zukunftsweisende Lösungen für die Integration von Motion Control in Bewegungsachsen. Die gesamte Technologie basiert auf dem SOMANET MOTION Software Stack. Synapticon ist das einzige "Software-First-Unternehmen" im Motion Control Bereich.
Digitalisierung
Per Software gesteuerte, adaptive Präzision sichert hohe Qualität der Motion Control
Miniaturisierung
Hochintegrierte, ultrakompakte Bauweise ohne Reduzierung der Leistung
Integration
Signifikant reduzierte Größe der Komponenten und gleichzeitig höhere Leistungsdichte
Synapticon SOMANET Motion Cores basieren auf xCore- und ARM-Prozessorarchitekturen und bieten 8 bis 32 programmierbare 32-Bit-RISC-Kerne pro Chip, die über einen Hochgeschwindigkeits-Echtzeit-Prozessorbus kommunizieren. Diese hochparallele, harte Echtzeit-Architektur ist die Grundlage der überlegenen Regelungsleistung von Synapticon und der fortschrittlichen Funktionen der SOMANET-Produkte.
MOTION CORESMotion Control der Zukunft
HÖHERER WIRKUNGSGRAD
Steigern des Wirkungsgrads durch Model-Predictive Deadbeat Field-Oriented Control (MPD Control) Technologie
REDUKTION DER WÄRMEABGABE
Gesteigerte Leistung im Vergleich zu anderen Anbietern durch viel geringere Wärmeentstehung.
1.X SCHALTZYKLEN BIS ZUM STEUERUNGSZIEL
Verwenden eines erweiterten Modells von Leistungselektronik, Motor, Untersetzung und Last, um das Steuerungsziel zu erreichen.
RICHTUNGSWEISEND BEI SERVOANTRIEBEN
Vergleichbare Stromregler benötigen mehrere Schaltzyklen, um ein gewünschtes Ziel zu erreichen bzw. führen wesentlich mehr Wärme ab.
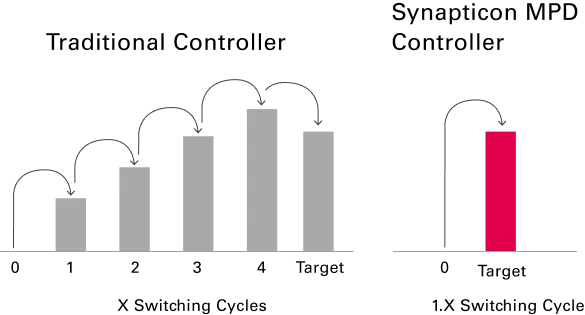
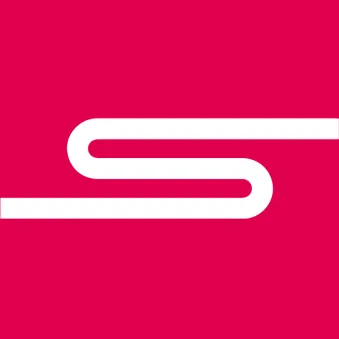
Mehr LEISTUNGSDICHTE für sichere Servoantriebe
Synapticon erweitert die Grenzen der im Smartphone-Design üblichen Mixed-Signal-Integration und High-Density-Interconnect-Technologie (HDI) und kombiniert sie mit jahrzehntelanger Erfahrung im Leistungsstufendesign.
- Ultrakompakte Servoantriebsdesigns
- Intelligente Steuerung von Wärmeableitung
- Gehäuselose EMV-Zertifizierung
- Gesamte erforderliche Funktionalität in einem Gerät
- Hohe Leistungsdaten in einer realistischen thermischen Integrationssituation
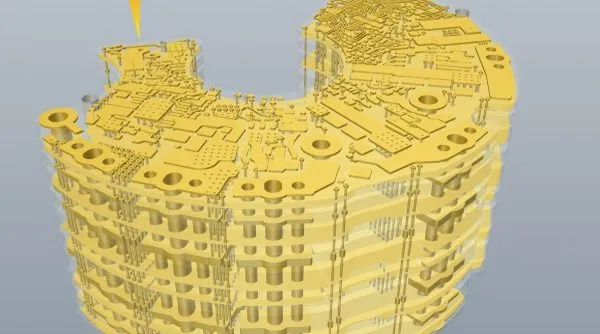
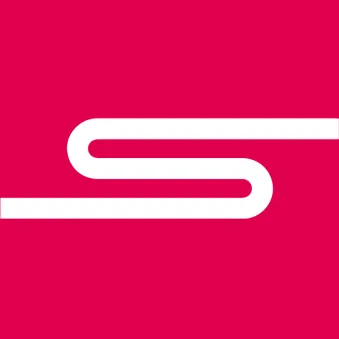
MOTION CONTROL TRIFFT DEN FUSIONSREAKTOR
Synapticon entfesselt die Kraft der Integration. Diskrete Komponenten, wie z.B. separate Servoantriebe, Positions-Feedback-Sensoren, Sicherheitsfunktionen und Bremsen, sind automatisch mit einem Overhead an Größe und Kosten verbunden, da mechanische und elektrische Schnittstellen die Kompatibilität zwischen einer breiten Palette von Geräten sicherstellen müssen. Hinzu kommt, dass die Interaktion zwischen den Geräten begrenzt ist.
In den Servoantrieb integrierte Positionsgeber sparen nicht nur erheblich Platz und Kosten: Der Zugriff auf mehr Daten durch die direkte Kopplung von Sensor-Lesekopf und Servoantriebs-CPU ermöglicht neue Möglichkeiten bei der Kalibrierung, so dass kostengünstige Encoder-Technologie eine High-End-Leistung bieten kann.
In den Servoantrieb integrierte Positionsgeber sparen nicht nur erheblich Platz und Kosten: Der Zugriff auf mehr Daten durch die direkte Kopplung von Sensor-Lesekopf und Servoantriebs-CPU ermöglicht neue Möglichkeiten bei der Kalibrierung, so dass kostengünstige Encoder-Technologie eine High-End-Leistung bieten kann.
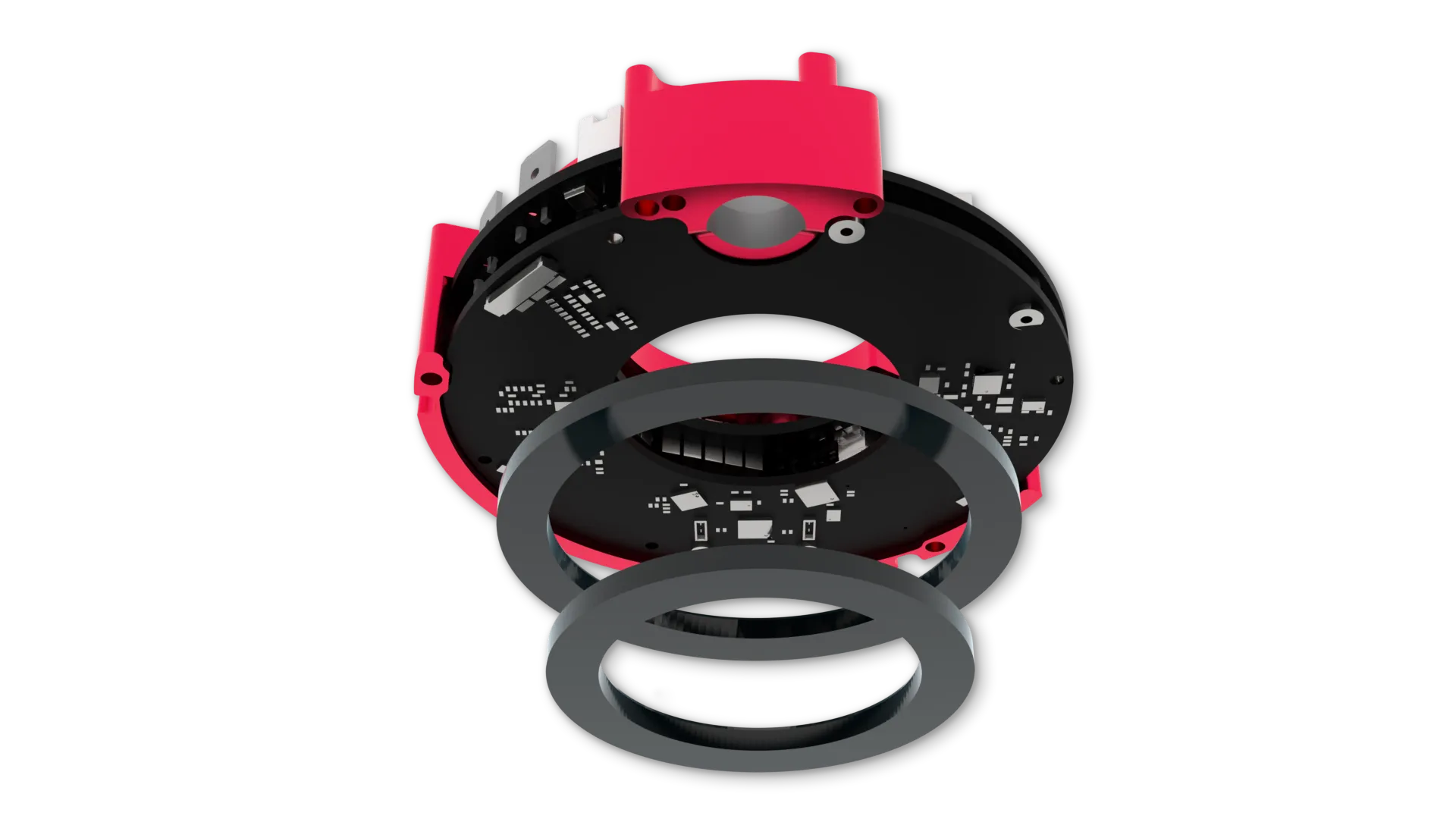
- Mehr Platz durch integrierte Positionsgeber
- Schnellerer Zugriff auf mehr Daten
- Direkte Kopplung von Sensor-Lesekopf und Serviantriebs-CPU
- Kostengünstige Encoder-Technologie
- High-End Motion Control System
- Integration auf kleinstem Raum
100%
PRODUCTS
CERTIFIED
CERTIFIED
Funktionale Sicherheit integriert: SOMANET SAFE MOTION
Alle SOMANET Produkte sind vollständig zertifiziert. Wir etablieren somit einen unerreichten Standard für sichere Applikationen wie Cobots und AGVs.
Stellen Sie sich AGV/AMR-Räder vor, die alles enthalten, was das mobile System zum sicheren Antrieb des Fahrzeugs benötigt. Synapticon ermöglicht eine schnelle und deutlich vereinfachte Entwicklung von Cobots.
Stellen Sie sich AGV/AMR-Räder vor, die alles enthalten, was das mobile System zum sicheren Antrieb des Fahrzeugs benötigt. Synapticon ermöglicht eine schnelle und deutlich vereinfachte Entwicklung von Cobots.
Die Integration der Sicherheitsfunktionalität direkt in die Antriebe hat mehrere Vorteile:
- Weniger Verkabelung – Keine langen Encoder-Kabel oder herkömmlichen Sicherheitskomponenten erforderlich
- Schnelle Reaktion – Entlasten des Sicherheitshandlings von der Sicherheits-SPS zu einzelnen Antrieben
- Schnellere Energiezyklen – Sichere Modi ohne Unterbrechung der Stromversorgung
- Erhöhte Produktivität – Zugriff auf die Maschine im Sicherheitsmodus ohne diese komplett herunterzufahren
- Kosteneinsparung – Im Vergleich zu herkömmlichen Sicherheitslösungen
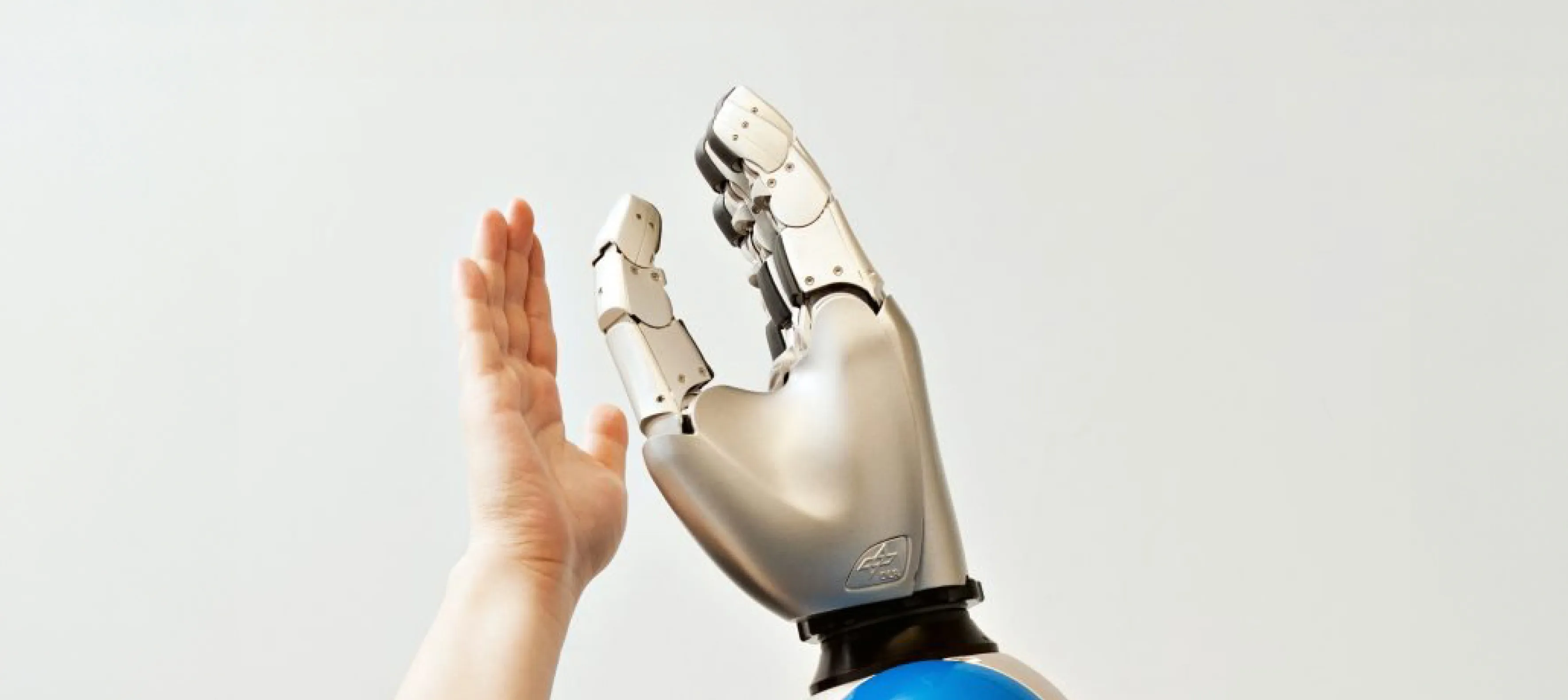
GETRIEBE:
DIE ULTIMATIVE CHALLENGE
Synapticon verbindet die Welten von Software, Elektronik und Mechanik. Getriebe sind nach wie vor die teuersten Komponenten in Hochleistungs-Motion-Control-Achsen, wie z.B. Gelenken von Industrierobotern. Sie sind auch die mechanischste Komponente jeder Bewegungsachse.
Robustheit, Zuverlässigkeit und Präzision werden heute im Wesentlichen durch den Produktionsaufwand erreicht. Nach jahrzehntelanger Optimierung können sprunghafte Verbesserungen nur erreicht werden, wenn wir bestehende Technologien in Frage stellen und über den Tellerrand hinausdenken.
Dies ist der Punkt, an dem die interdisziplinären Fähigkeiten von Synapticon ihre volle Wirkung entfalten. Die digitale Getriebesteuerungstechnologie von Synapticon definiert die grundlegende Zusammensetzung von Bewegungsachsen neu. Das ermöglicht die dynamische Steuerung von Parametern, die bisher statisch waren. Fortsetzung folgt.
Robustheit, Zuverlässigkeit und Präzision werden heute im Wesentlichen durch den Produktionsaufwand erreicht. Nach jahrzehntelanger Optimierung können sprunghafte Verbesserungen nur erreicht werden, wenn wir bestehende Technologien in Frage stellen und über den Tellerrand hinausdenken.
Dies ist der Punkt, an dem die interdisziplinären Fähigkeiten von Synapticon ihre volle Wirkung entfalten. Die digitale Getriebesteuerungstechnologie von Synapticon definiert die grundlegende Zusammensetzung von Bewegungsachsen neu. Das ermöglicht die dynamische Steuerung von Parametern, die bisher statisch waren. Fortsetzung folgt.
Zukunftsweisend
Dynamische Steuerung von Parametern
Interdisziplinär
Verbindung von Software, Elektronik und Mechanik
Zuverlässig
Robuste und präzise Technologie
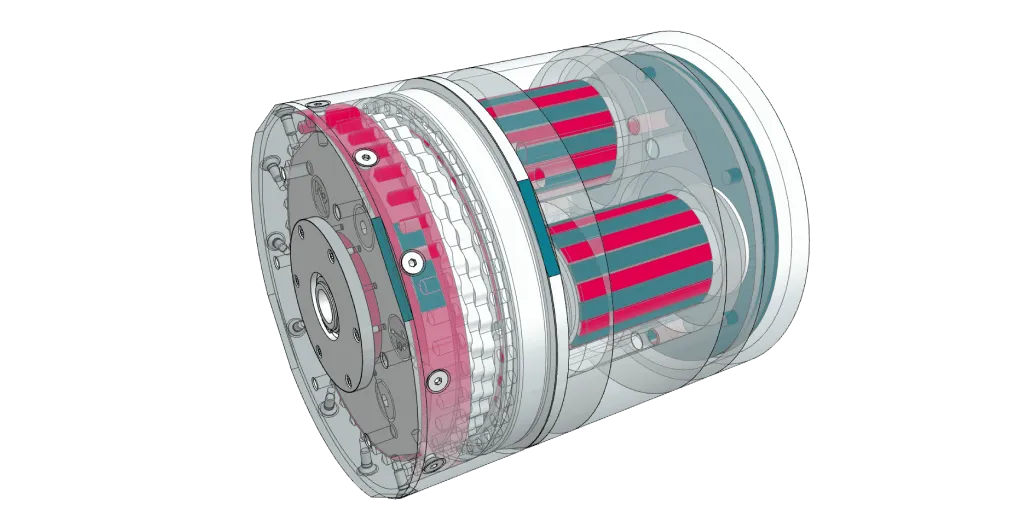
NEWSLETTER
Verpassen Sie kein Update mehr. Der Synapticon-Newsletter informiert Sie als erstes über Neuigkeiten rund um unsere Produkte.
SIE HABEN NOCH OFFENE FRAGEN?
Wir beraten Sie gerne zu Ihren Nutzungsmöglichkeiten des Circulo. Sprechen Sie mit unsüber Ihr Projekt in jedem Entwicklungsstadium.