SOMANET
SAFE MOTION
MEHR SICHERHEIT BEI
ANTRIEBSREGELGUNGEN
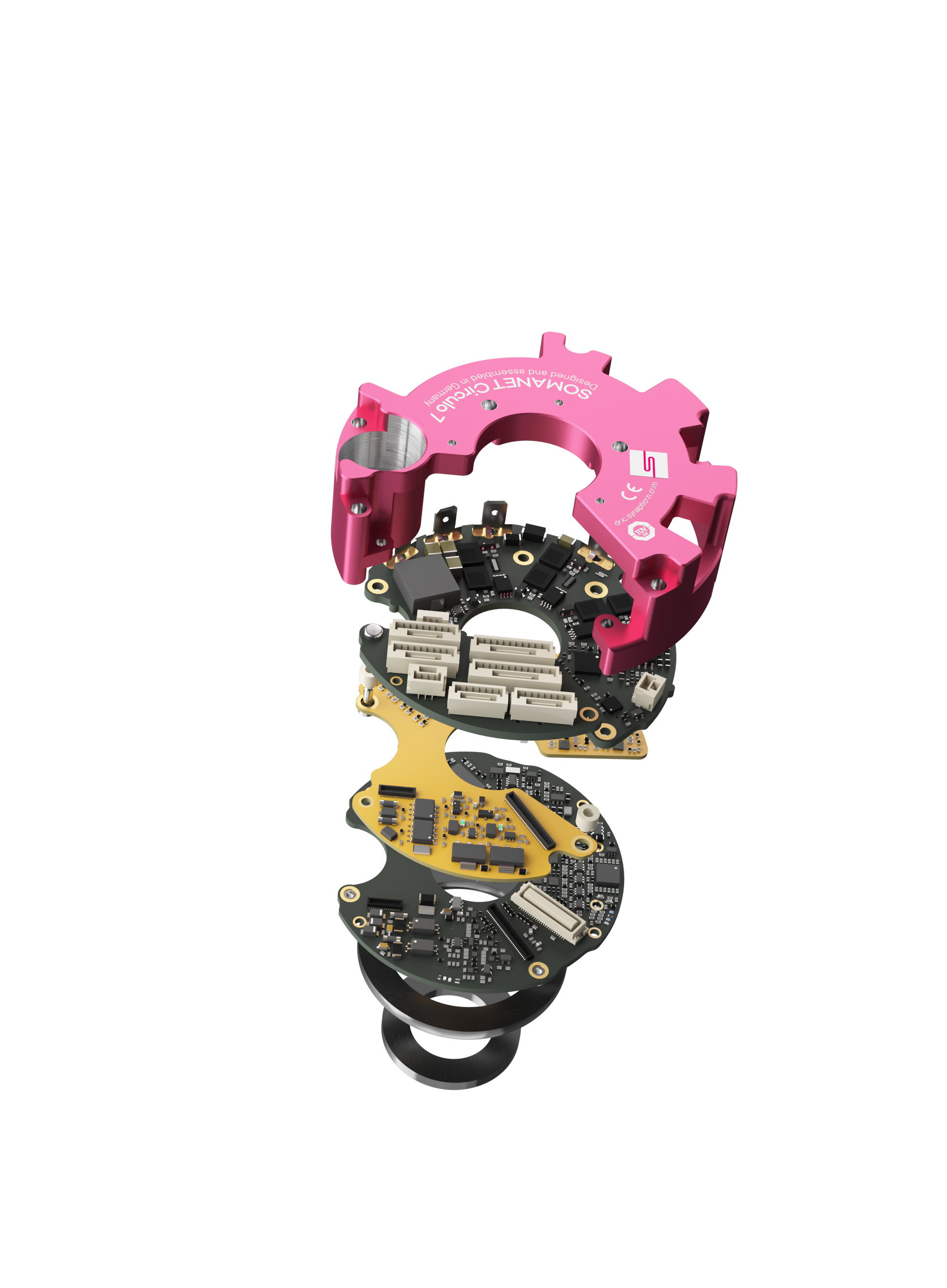
CERTIFIED
SOMANET Safe Motion ist physisch zwischen dem Prozessormodul und dem Antriebsmodul montiert. So kann die Sicherheitserweiterung sicherheitskritische Signale überwachen generieren und empfangen, ohne dass die vorhandene Hardware geändert oder eine komplexe Verkabelung der Lösung vorgenommen werden muss. SOMANET Safe Motion bietet Sicherheitsfunktionen wie STO, SBC, SS1, SS2, SLS, SLP, SLT, die alle über FSoE oder I/O verfügbar sind.
Downloads
ETHERCAT CONFORMANCE
CERTIFIED
DIE ZUKUNFT FÜR ECHTE MENSCH-ROBOTER-KOLLABORATION
STO verhindert ein ungeplantes Wiederanlaufen des Laufwerks. STO ermöglicht sicheres Arbeiten und hat ein breites Einsatzspektrum bei bewegten Achsen.
SBC ermöglicht die sichere Ansteuerung einer Haltebremse. Die Funktion wird immer parallel zu STO aktiviert und mit STO oder SS1 verwendet. Das verhindert die Bewegung einer Achse im drehmomentfreien Zustand.
...
Die SS1-Funktion bewirkt ein schnelles und sicheres Anhalten des Motors und führt zu einem Stillstand.
Die SS2-Funktion schaltet einen Motor schnell und sicher ab. Wenn der Motor stillsteht, wird ein sicherer Betriebsstopp (SOS) ausgelöst.
SLS stellt sicher, dass der Antrieb eine definierte Drehzahlgrenze nicht überschreitet und löst bei Überschreiten eine Fehlerreaktion aus.
Die Sicherheitsfunktion überwacht, dass der Antrieb (und damit das vom Antrieb bewegte Element) definierte Endlagen nicht überschreitet.
Sicher begrenztes Drehmoment. Die Funktion SLT ermöglicht die Reduzierung des Drehmomentes innerhalb einer definierten Zeit.Wenn das Drehmoment die SLT-Überwachungsgrenze überschreitet, reagiert derAntrieb mit einem "sicheren Stopp".
via FSoE (7 ms cycle time)
via FSoE (7 ms cycle time)
via FSoE (7 ms cycle time) - beim Anschluss eines sicheren Torque Sensors am sicheren analogen Eingang.
via FSoE (7 ms cycle time)
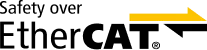
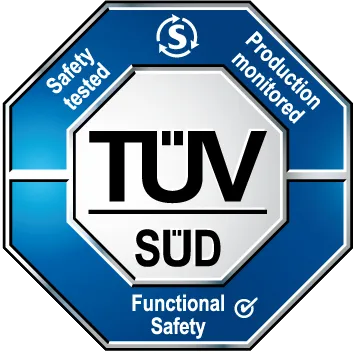
SAFETY FIRST
Das optionale Safe-Motion-Modul für Circulo ermöglicht sichere Bewegungsfunktionen auf SIL3, PL-e Niveau über FSoE (FailSafe over EtherCAT). Realisieren Sie Ihre Applikation gemäß ISO/TS 15066.
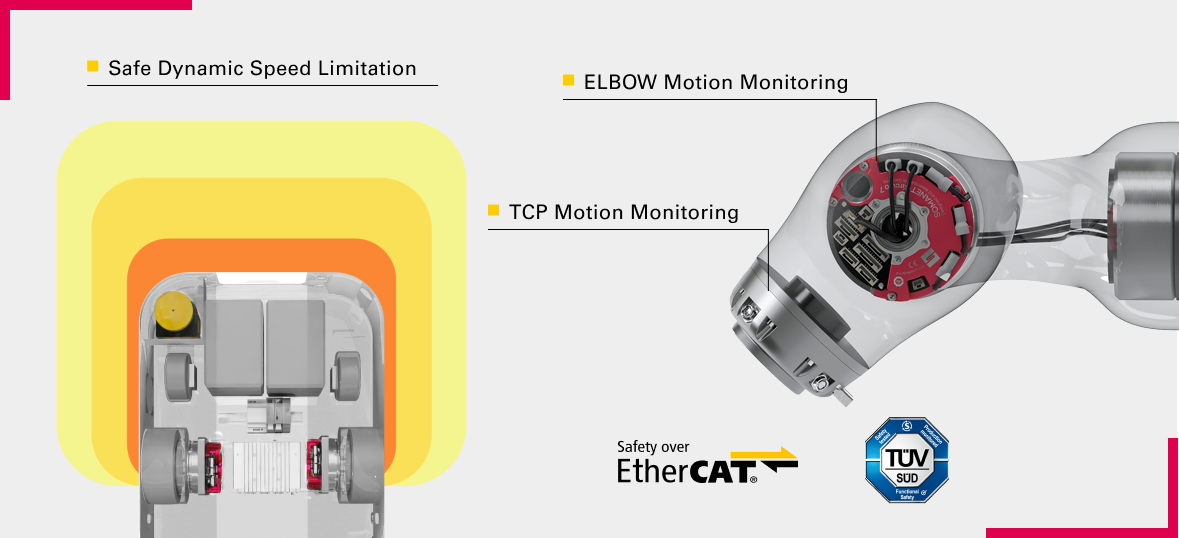
FSoE KommuniKation
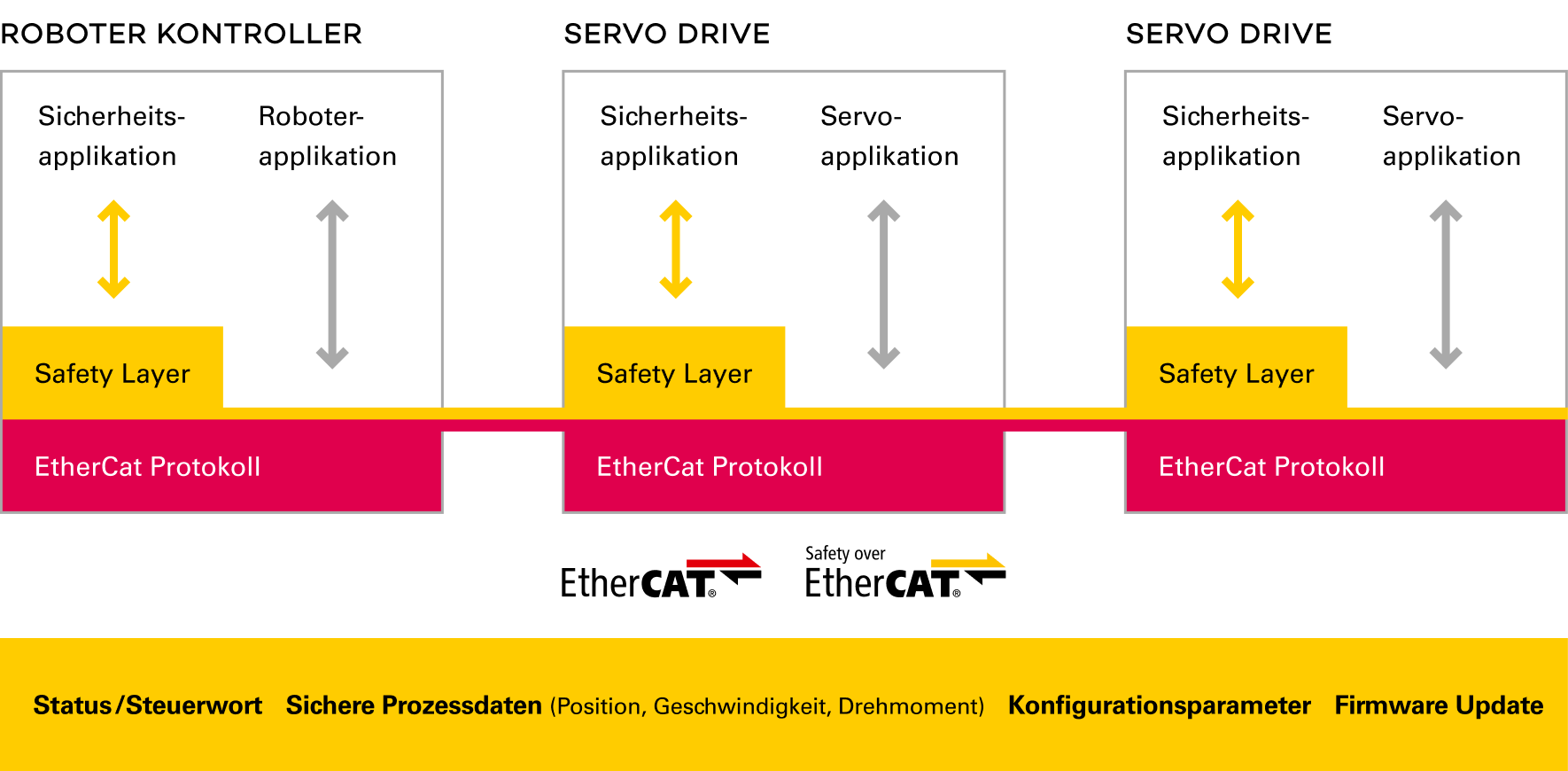
SOMANET Integrated Brake System
- Die Motordrehzahl wird auf ein niedriges Niveau reduziert, bevor die Bremse einrastet.
- Die Bremse verhindert eine ungewollte Drehbewegung des Motors (z. B. bei Stromausfall).
- Dadurch verhindert der Servo-Drive einen unerwünschten Kontakt mit dem zu bearbeitenden Werkstück bzw. zwischen Roboter und Mensch.
ANWENDUNGEN
SOMANET SAFE MOTION
Das erfordert ein neues Niveau der intrinsischen funktionalen Sicherheit von Robotern. Gerade bei begrenzter Produktionsfläche profitieren Sie von fortschrittlichen Sicherheitskonzepten. Dank SOMANET Safe Motion benötigen Sie keine Roboterkäfige mehr.
Und in Folge der sicheren und gesicherten Bewegungssteuerung lassen sich heute Systemdesigns realisieren, die Wartungsvorgänge bei laufendem Betrieb erlauben. Unterbrechen der Produktivität ist „old school“. Das Senken der Gesamtbetriebskosten ist der „new deal".
SIE HABEN NOCH FRAGEN?
Sprechen Sie mit uns über Ihr Projekt in jedem Entwicklungsstadium.