SOMANET für
AGV und AMR
DIE ALL-IN-ONE-LÖSUNG für AGV
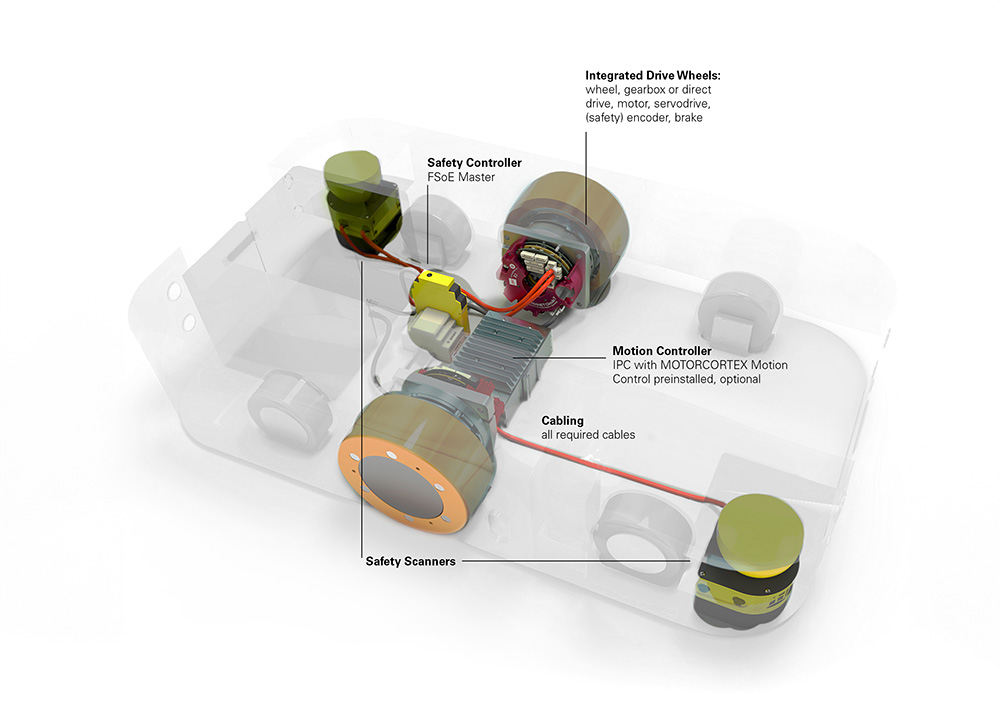
Entdecken Sie jetzt die Turnkey Solution für AGV und AMR. Ein komplettes Kit bestehend aus Integrated Drive - Rad, Safety Controller, Motion Controller IPC, Safety Scannern sowie der kompletten Verkabelung
AGV TURNKEY SOLUTIONWARTUNG
VORTEILE des
„NEXT-GEN“ AGV
SOMANET Lösungen für für AGV/AMR Applikationen bringen viele Vorteile mit sich. Die All-in-One AGV Axis Solution von Synapticon vereint Räder, Motor, Servoantrieb, Encoder und optional die Functional Safety mit integrierter Bremse in in einer einzigen Einheit. Das vereinfacht die Entwicklung deutlich, senkt den Produktionsaufwand sowie die Produktionskosten. Auch die Wartung ist weitaus weniger komplex.
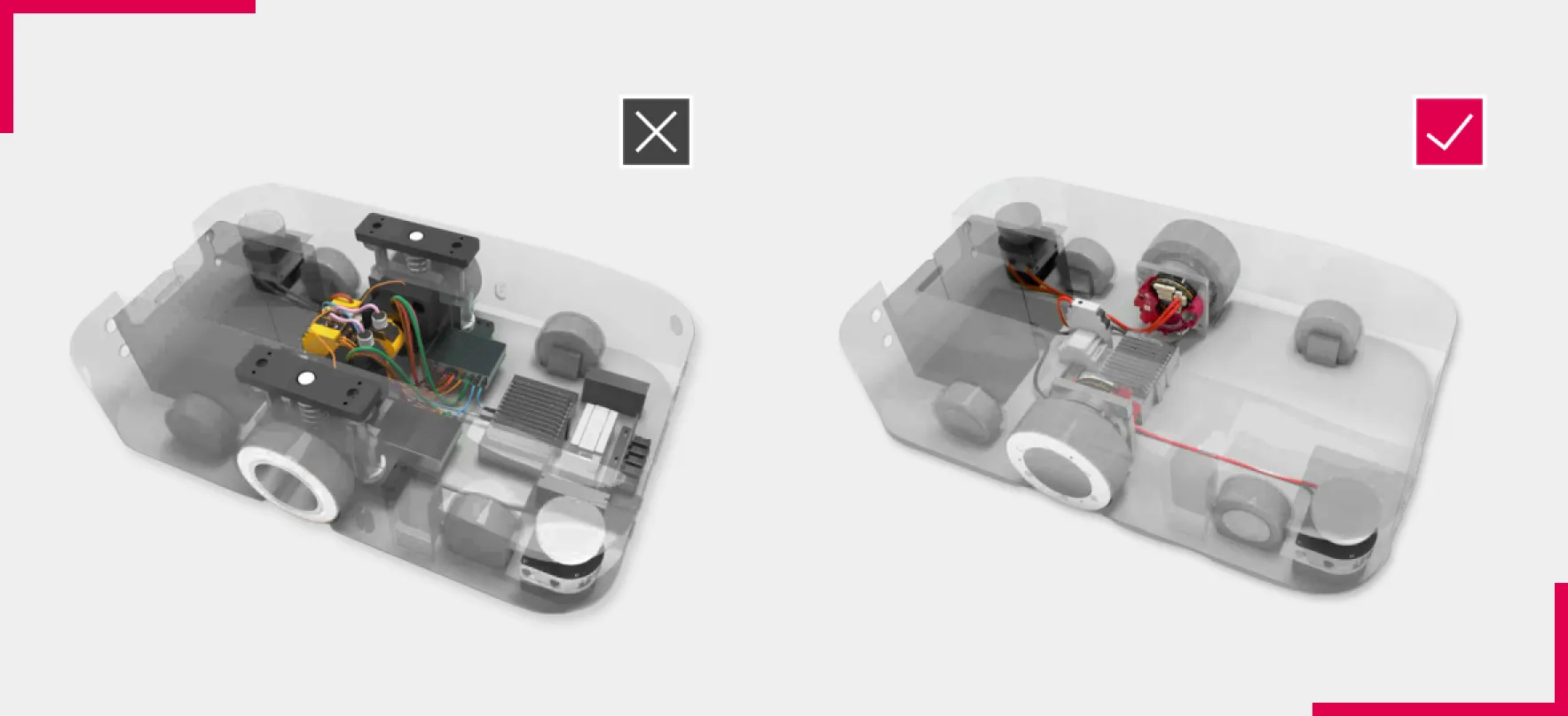
- Geringere Komplexität des Systems
- Mehr Platz für Batterien
- Schnelle Wartung
- Weniger Systemausfälle
- Kürzere Entwicklungszeit
- Längere Laufzeiten
- Kürzere Stillstandzeiten
- Weniger Komponenten bei gleicher Funktionalität
EINFACHES
KABEL-MANAGE-MENT
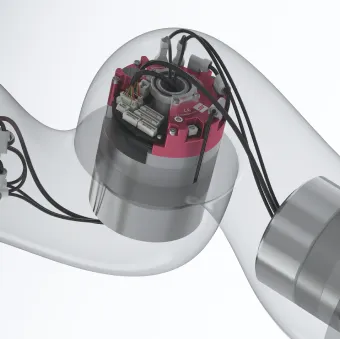
Spart Kosten und viel Platz im Inneren des AGV.
Sichere und zuverlässige Umgebung im AGV oder AMR.
DEMO ANFORDERN
INTEGRIERTES BREMSSYSTEM
Der Verriegelungsmagnet des SOMANET Integrated Brake Systems wird nur aktiviert, wenn der Motorantrieb deaktiviert ist oder im Falle eines Notstopps.
Dieses Bremssystem wirkt wie eine Haltebremse und verhindert so jede Bewegung des AGV. Das vermeidet unerwünschte Bewegungen des AGV und garantiert einen sicheren Stopp.
CERTIFIED
DIE ZUKUNFT FÜR ECHTE MENSCH-ROBOTER-KOLLABORATION ist jetzt
STO verhindert ein ungeplantes Wiederanlaufen des Laufwerks. STO ermöglicht sicheres Arbeiten und hat ein breites Einsatzspektrum bei bewegten Achsen.
SBC ermöglicht die sichere Ansteuerung einer Haltebremse. Die Funktion wird immer parallel zu STO aktiviert und mit STO oder SS1 verwendet. Das verhindert die Bewegung einer Achse im drehmomentfreien Zustand.
...
Die SS1-Funktion bewirkt ein schnelles und sicheres Anhalten des Motors und führt zu einem Stillstand.
Die SS2-Funktion schaltet einen Motor schnell und sicher ab. Wenn der Motor stillsteht, wird ein sicherer Betriebsstopp (SOS) ausgelöst.
SLS stellt sicher, dass der Antrieb eine definierte Drehzahlgrenze nicht überschreitet und löst bei Überschreiten eine Fehlerreaktion aus.
Die Sicherheitsfunktion überwacht, dass der Antrieb (und damit das vom Antrieb bewegte Element) definierte Endlagen nicht überschreitet.
Sicher begrenztes Drehmoment. Die Funktion SLT ermöglicht die Reduzierung des Drehmomentes innerhalb einer definierten Zeit.Wenn das Drehmoment die SLT-Überwachungsgrenze überschreitet, reagiert derAntrieb mit einem "sicheren Stopp".
via FSoE (7 ms cycle time)
via FSoE (7 ms cycle time)
via FSoE (7 ms cycle time) - beim Anschluss eines sicheren Torque Sensors am sicheren analogen Eingang.
via FSoE (7 ms cycle time)
SAFETY FIRST
Das optionale Safe-Motion-Modul für Circulo ermöglicht sichere Bewegungsfunktionen auf SIL3, PL-e Niveau über FSoE (FailSafe over EtherCAT). Realisieren Sie Ihre Applikation gemäß ISO/TS 15066.
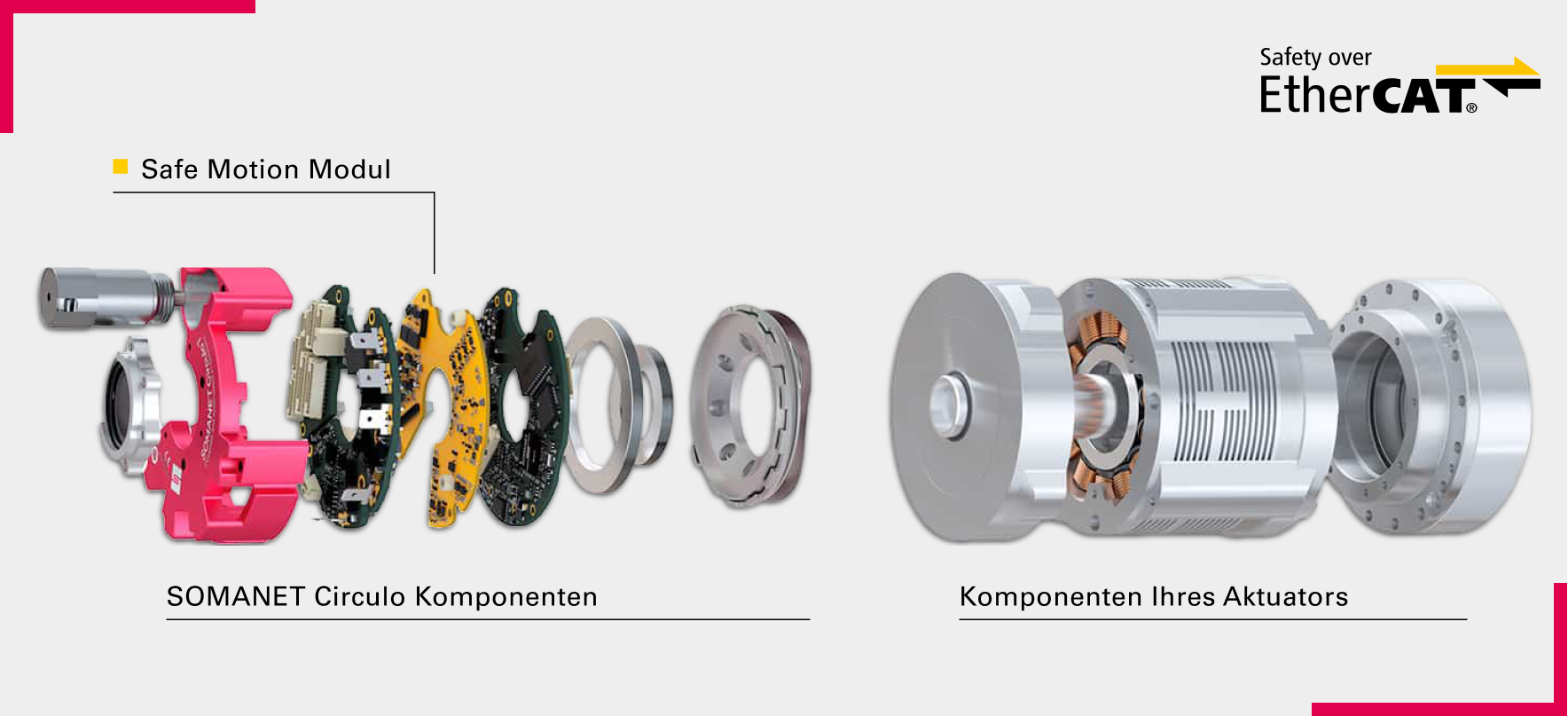
VORGESTELLTE KUNDENPRODUKTE
Sprechen Sie mit uns, wir erläutern Ihnen gerne mehr Details.