SOMANET
NODE
Höchste Stromdichte
für maximale Leistung
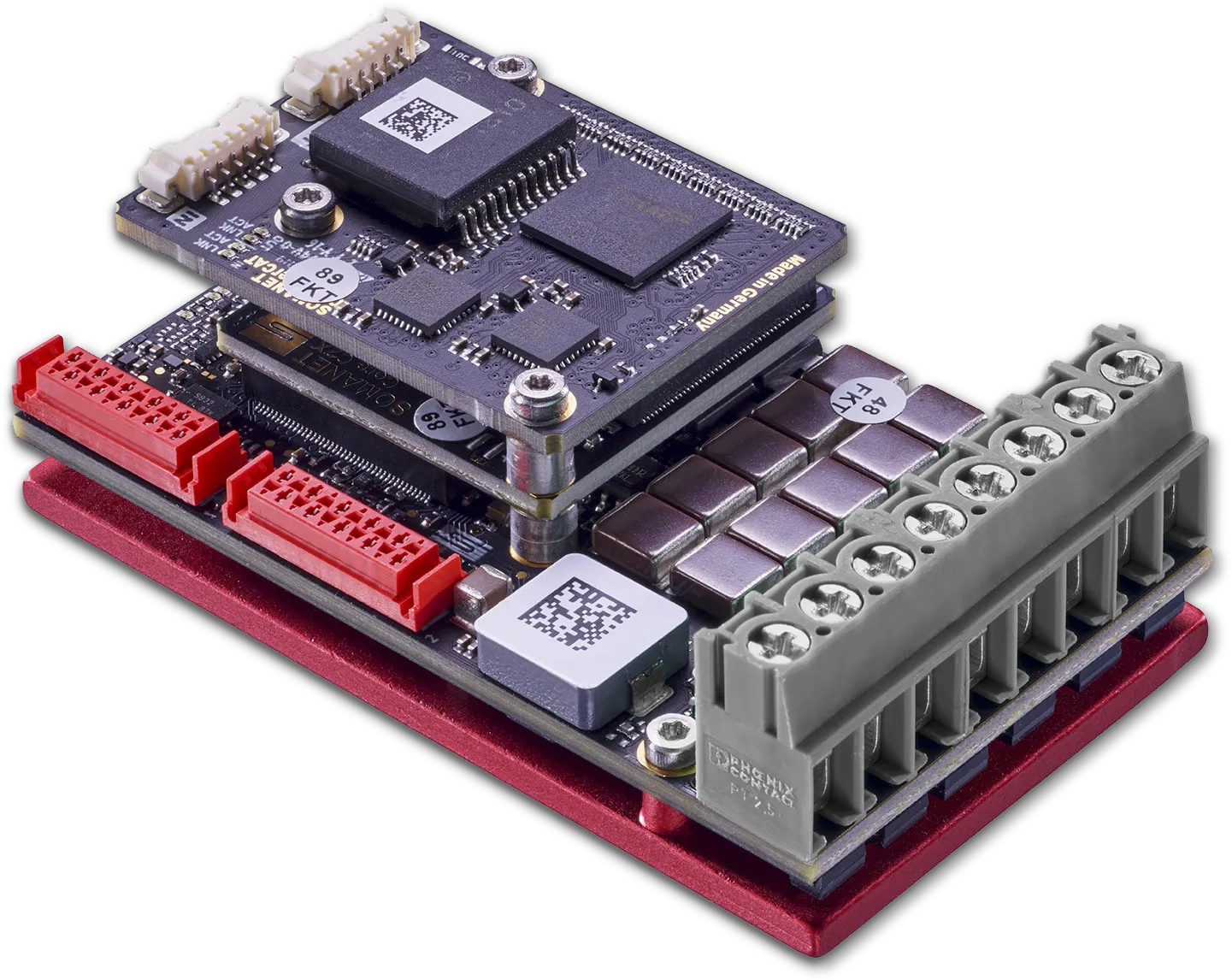
Die kompakten und effizienten Servoantriebe SOMANET Nodes übertreffen in ihrer Leistungsdichte vergleichbare Produkte um ein Vielfaches. Sie unterstützen alle PMSM-, Synchron-AC- und BLDC-Motoren bis 60 V und 100 A / 66 A_rms und verfügen über eine EtherCAT-Schnittstelle mit CiA DS 402-Protokoll.
SOMANET Nodes steigern dank intelligenter Algorithmen die Leistung von Motoren und Getrieben in Ihren Antriebsregelungen. Dabei ermöglichen sie präzise und gleichzeitig schnelle Bewegungen Ihrer Roboter und können Lage, Position, Geschwindigkeit und Beschleunigung eines Roboterarms präzise regulieren.
Alle Funktionen der SOMANET Node Serie sind kompatibel mit OBLAC Tools, einer einfach zu bedienenden und dennoch leistungsstarken Tool-Suite zur Inbetriebnahme und Bewegungsabstimmung.
PRODUKTDEMO BUCHENSOMANET Nodes steigern dank intelligenter Algorithmen die Leistung von Motoren und Getrieben in Ihren Antriebsregelungen. Dabei ermöglichen sie präzise und gleichzeitig schnelle Bewegungen Ihrer Roboter und können Lage, Position, Geschwindigkeit und Beschleunigung eines Roboterarms präzise regulieren.
Alle Funktionen der SOMANET Node Serie sind kompatibel mit OBLAC Tools, einer einfach zu bedienenden und dennoch leistungsstarken Tool-Suite zur Inbetriebnahme und Bewegungsabstimmung.
Maximale Power
für Servoantriebe
HÖCHSTE STROMDICHTE AM MARKT
Einzigartige Leistungsstärke bei minimaler Wärmebildung.
UNÜBERTROFFENE INTEGRATIONSUNTERSTÜTZUNG
Die maximale Leistungsabgabe meist viel höher dank optimaler Integration.
HOCHENTWICKELTE STÖRUNGSKOMPENSATION
Erkennt Sensorrauschen, Nichtlinearitäten in Motor und Getriebe sowie Rastmoment.
Rahmenlose EMV
Elektromagnetische Verträglichkeit, Fähigkeit eines technischen Geräts, andere Geräte nicht durch ungewollte elektrische oder elektromagnetische Effekte zu stören oder durch andere Geräte gestört zu werden.
ZERTIFIZIERTE FUNKTIONSSICHERHEIT
Verfügt über TÜV-zertifizierte STO- und SBC-Funktionen auf SIL3 PLe-Niveau.
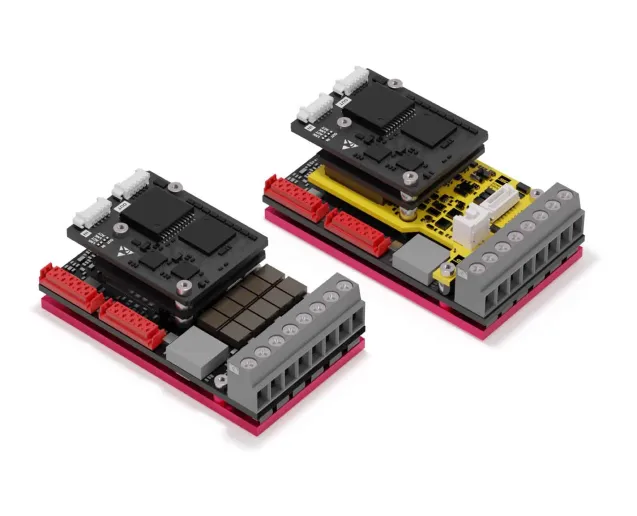
ULTRA KOMPAKT
Abschaffung des Schaltschranks, massive Kabeleinsparung und deutlich reduzierte Komplexität der Anwendung.
Vielseitig
3 Module eines SOMANET
Nodes in mehreren in mehreren Leistungsstufen sowie grundlegenden Safety-Funktionen.

EFFIZIENT
Ruhig laufende Antriebe mit geringer Wärmeleistung bei gleichzeitig sehr hoher Bewegungsregelungsleistung.
Servoantrieb in 3 Modulen
Ein SOMANET Node besteht aus drei Modulen: Kommunikations- (Com), Prozessor- (Core)
und Antriebsmodul. Für jedes dieser Module stehen mehrere Standardoptionen zur Verfügung. Auf Anfrage entwickeln wir für Sie auch kundenspezifische Module.
SOMANET Node Safety verfügt zusätzlich über TÜV-zertifizierte STO- und SBC-Funktionen auf SIL3 PLe-Niveau.
SOMANET Node Safety verfügt zusätzlich über TÜV-zertifizierte STO- und SBC-Funktionen auf SIL3 PLe-Niveau.
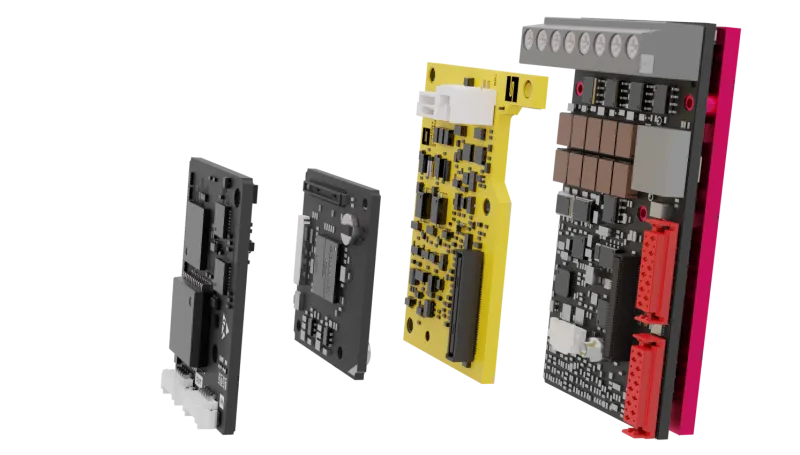

- Reduziert die Anzahl der Kabel von 100 auf 6
- Vereinfacht Ihr Produktionsdesign
- Verringert die Kosten für Ihre Roboter- oder Maschinensysteme
- Lässt sich durch zusätzliche Sicherheitsfunktionen oder Sensoren erweitern
INTELLIGENTE ALGORITHMEN
für maximale EFFIZIENZ
Erleben Sie Motorphasenüberwachung in hoher Geschwindigkeit und hoher Auflösung. So funktioniert Motion Control der Zukunft. Das SOMANET Software Stack bietet einen Modell-prädiktiven feldorientieren Regelungsansatz: Model Predicitve Deadbeat Control.
Dank dieser Technologie erreichen Sie perfekt gleichmäßig und ruhig laufende Antriebe mit einer geringen Wärmeabgabe.
Dank dieser Technologie erreichen Sie perfekt gleichmäßig und ruhig laufende Antriebe mit einer geringen Wärmeabgabe.
PERMANENTE KONTROLLE
Berechnet durchgängig die Abläufe im angeschlossenen Motor.
FLEXIBLE REAKTION
Kann spontan aus einem Spektrum an Regelungsstrategien auswählen.
MAXIMALE ANPASSUNGSFÄHIGKEIT
Passt sich der aktuellen Belastungssituation an.
OPTIMALE MOTORPHASENSTEUERUNG
Reagiert auf die exakte Motorgeometrie.
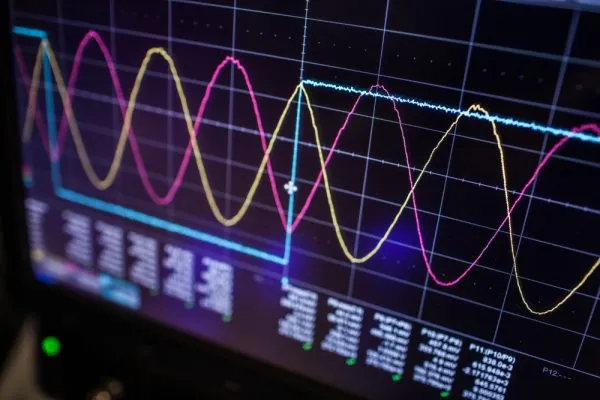
KLEIN-SPANNUNG
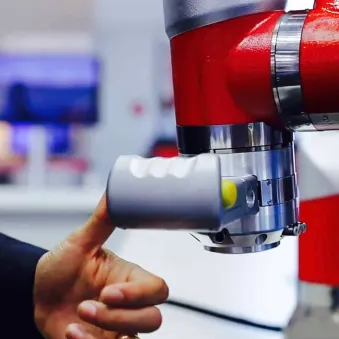
Sichere Spannung geht
vor hoher Spannung.
Nur so arbeiten kollaborative
Roboterarme eigensicher.
Synapticons Frequenzumrichter
arbeiten daher mit
den modernsten
Leistungshalbleitern
auf dem Markt.
SOMANET NODES FÜR ZUKUNFTSWEISENDE ROBOTIK
Mit den SOMANET Nodes verwirklichen Sie ein einfacheres Produkt-Design. Erleben Sie maximale Leistung mit der höchstmöglichen Stromdichte. Sparen Sie Zeit und Kosten.
MEHR INTELLIGENZ
IN ServoANTRIEBEN
Synapticons Antriebe können mit einer große Anzahl an Feedback-Encodern, Drehmoment- und Kraftsensoren kommunizieren. Die Synapticon Nodes reagieren auf berührungsempfindliche Häute und interpretieren LiDAR Daten (kundenspezifische Lösungen).
Unsere Servo-Drive-Systeme lassen sich mit Ihrer eigenen Software lokal kombinieren. So können Sie Reflexe auf Basis von Sensorsignalen und andere kundenspezifische Algorithmen direkt auf dem Antrieb implementieren.
Unsere Servo-Drive-Systeme lassen sich mit Ihrer eigenen Software lokal kombinieren. So können Sie Reflexe auf Basis von Sensorsignalen und andere kundenspezifische Algorithmen direkt auf dem Antrieb implementieren.
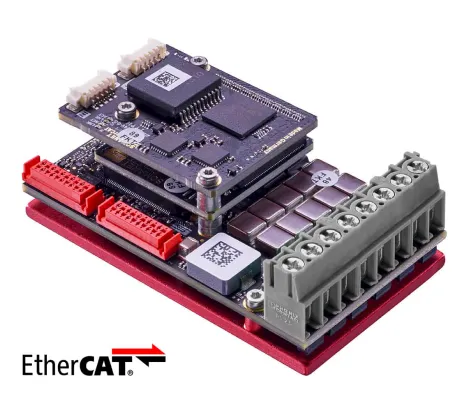
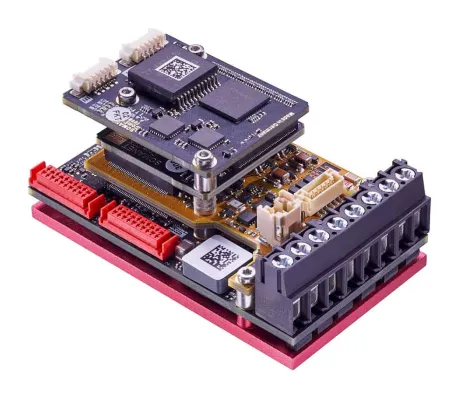
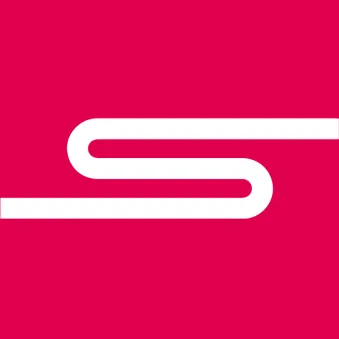
STARTEN SIE MIT EINEM EVALUIERUNGSKIT
Die einfachste Art, SOMANET Servoantriebe zu evaluieren.
Testen Sie die SOMANET Nodes mit Permanentmagnet-Synchronmoto-ren (PMSM/BLDC) verschiedener Baugrößen bis 2000 W (48 V / 66 Arms) und integrieren Sie diese als Slaves in Ihr EtherCAT-System.
Testen Sie die SOMANET Nodes mit Permanentmagnet-Synchronmoto-ren (PMSM/BLDC) verschiedener Baugrößen bis 2000 W (48 V / 66 Arms) und integrieren Sie diese als Slaves in Ihr EtherCAT-System.
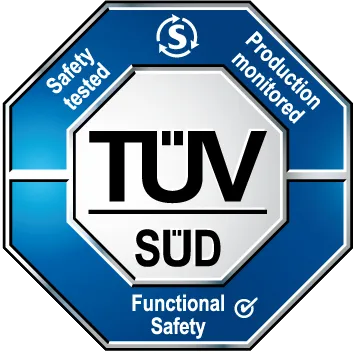
Das Kit enthält:
- Ein SOMANET Node mit der gewünschten Nennleistung (20 – 100 A)
- Kabel
- Eine handliche Box
- Eine OBLAC Drive Box (optional)
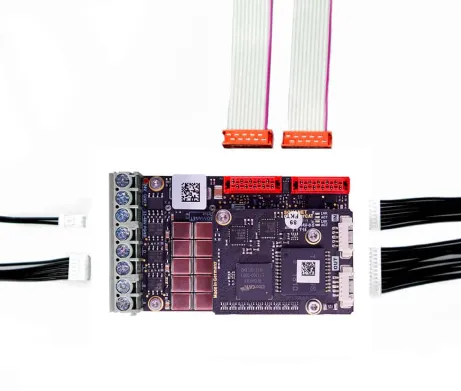
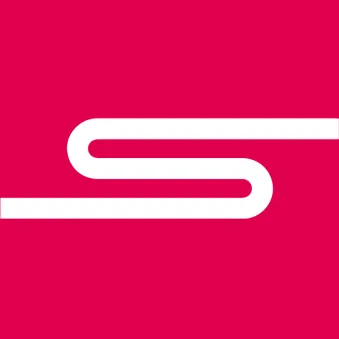
INTEGRATION in Motion-Control-Systeme
Servoantriebe ermöglichen es Robotern, präzise und schnelle Bewegungen auszuführen. Darum kommen sie in vielen Branchen wie zum Beispiel in der Automobil-, Elektronik- oder Verpackungsindustrie zum Einsatz.
OBLAC KONFIGURATIONS-
& TUNING-TOOL
Optimieren und kommissionieren Sie die Synapticon SOMANET Nodes mit unseren OBLAC Drive Tools. So arbeiten unsere Servo Drives mit Permanentmagnet-Synchronmotoren, Wechselstrommotoren oder bürstenlosen Gleichstrommotoren bis zu 60 V Nennspannung beliebiger Hersteller.
Synapticons OBLAC Drives Tools erleichtert die Konfiguration und Optimierung eines SOMANET Node für die Regelung von PMSM-, Synchron-AC- sowie BLDC-Motoren bis 60 V und 100 A / 66 Arms eines jeden Herstellers und Feedback-Sensors.
Synapticons OBLAC Drives Tools erleichtert die Konfiguration und Optimierung eines SOMANET Node für die Regelung von PMSM-, Synchron-AC- sowie BLDC-Motoren bis 60 V und 100 A / 66 Arms eines jeden Herstellers und Feedback-Sensors.
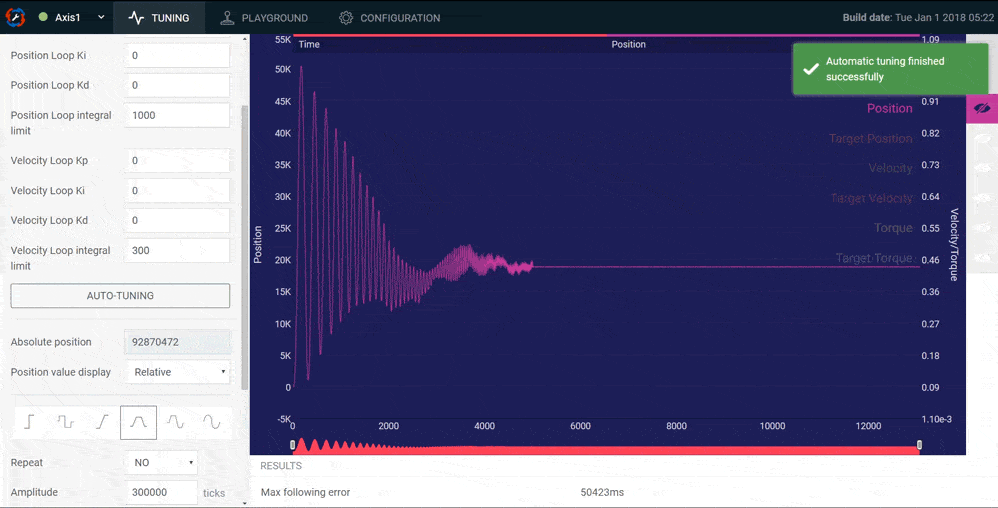
SIE HABEN NOCH OFFENE FRAGEN?
Wir beraten Sie gerne zu Ihren Nutzungsmöglichkeiten des Circulo. Sprechen Sie mit unsüber Ihr Projekt in jedem Entwicklungsstadium.